株式会社アバージェンス
マネジャー
佐々木 基公
半導体供給不足によるサプライチェーンの混乱
プロジェクト開始時はCOVID-19パンデミックの影響により、製造メーカーのサプライチェーンが大いに混乱していた時期でした。工場閉鎖およびIT化の加速による“受給のアンマッチ”、港湾閉鎖による“物流の停止”により、半導体メーカー・商社から製造メーカーへのデコミットが発生。
デコミットとは、予定していた納期日に部品が届かないことですが、1品種でもこれが発生した場合には、モノが作れず、届くまでその他は製品化が出来ず、生産拠点のキャッシュフローを大いに悪くすることになります。この1品種がもし、製品プラットホームに使用されるような部品であった場合には、複数モデルにまたがる為、その影響は甚大です。現在そのようなデコミットは落ち着きつつあるものの、半導体については、長期リードタイムでの購入を余儀なくされているというところが現状ではないでしょうか。
安全信頼のレガシィ部品と高アベイラビリティの新規部品の狭間で
部品製造を事業とするクライアント側の課題として、手に入りにくいレガシィ部品が多く使用されているという点がありました。型番が古く回路幅が広いレガシィ部品は、サプライヤーが増産体制を組まず、むしろEOL(End Of Life:製品提供/サポート終了)のリスクが高いです。
生産・出荷を安定させる為には、型番が新しく回路幅が狭い新規部品を採用することが望ましいのですが、日本企業の主力産業である自動車業界など、高い安全性を要求されるような製品を供給する場合には、過去に問題無く使えたレガシィ部品が好まれる傾向があります。しかし大手の半導体製造専門企業では一桁ナノの回路幅が狭い半導体製品が主力であり、回路幅の広いレガシィ部品は今後も大幅な増産体制は見込めない為、供給が限定される恐れがあるのです。
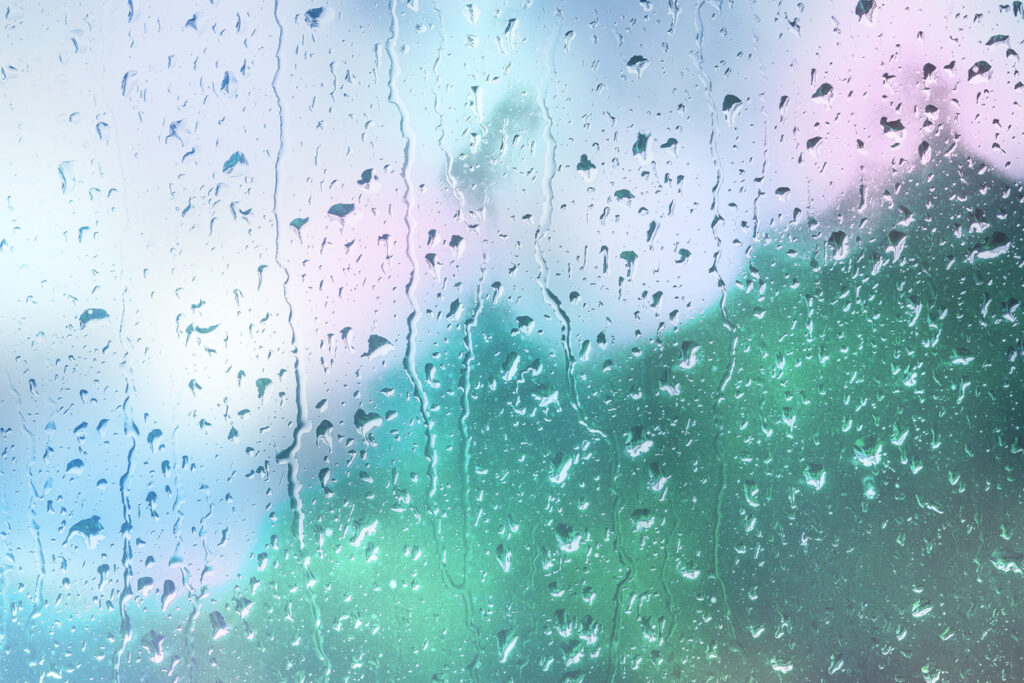
柔軟なサプライチェーン構築
要するに、自動車産業を中心とした高い安全性が要求される製造メーカーは、リードタイムが長く供給に制約のある部品を継続的に使用せざるを得ないという先行き不透明な中で、より柔軟なサプライチェーンを構築しなくてはならない状況にありました。当然、私が担当した部品製造業のクライアントも、供給・生産制約、市場制約を考慮した生産計画の策定、計画変動へ追従する業務プロセスづくり、迅速な設計変更を含めたサプライチェーン構築が急務でした。
最初はみな他人事
サプライチェーン構築は販売・生産管理・調達・生産拠点等、部門横断で取組む必要があります。一方、需要発生から製品供給までに変数が多く、どこに課題があって、どんな手を打つのが有効なのかが見えにくい為、「自部署は頑張っているが、他部署が…」となりやすい、つまり課題が他人事になりやすい傾向があります。私が担当したクライアントでも同じでした。
私が担当したプロジェクトでは、このサプライチェーン構築におけるありがちな課題を解決することから始める必要がありました。サプライチェーンの上流から下流までを対象に課題を構造化した上で、“皆が自責で考える”ことがあるべき姿である、と関係者全員に納得してもらう…。言葉にするのは簡単ですが、実現するのは容易でありません。しかし、考えれば考えるほど、そこから始めるべきという想いが強くなり、それが確信となり、プロジェクトをそう組み立てました。
喧々諤々の協議によるサプライチェーンのありたい姿構築
まず初手として、他部署・自部署を問わずに関係者全員を巻き込んで協議を進めていきました。通常業務で感じている他部署への要望や不満などを遠慮なく開陳していただきつつ、解決すべき項目を明確化して合意を形成することを繰り返し、課題の全体像を徐々に明らかにしていきました。
誰しも自分なりに一生懸命に仕事をしています。頑張っていない人なんていないと思います。これまでもずっと改善に次ぐ改善に取り組んできているはずです。
ただ、そうだからこそ、“ここを変えていこう”という前向きな意見に対して、“その課題解決に似たようなことは既にやっている”、“これ以上の改善は難しい”、という反応が出がちです。私たちはこれを「思い込みの支配」と呼んでいます。これまで様々な改革プロジェクトに伴走してきていますが、「思い込みの支配」は必ずあります。“常に努力している”という考えが既成概念化し、“だからこれ以上は無理”という発想に至ってしまう。ある意味、自然なことです。しかしそれは打破しなければなりません。
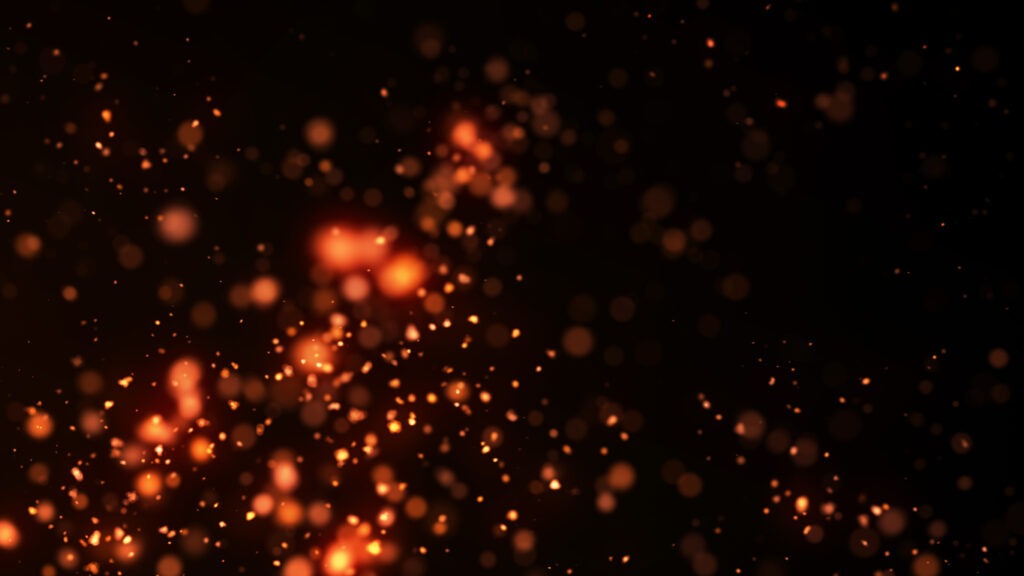
この打破に必要なことが2つあります。“可変的な点を明らかにする”、“工数的な制限をいったん無視して考える”、です。
“可変的な点を明らかにする”ためには、現行業務の中で課題の全てにアプローチ出来ているのか、それらは効果的なアプローチなのか、定常的に実施出来ているのか、という問いを何層にも重ねていくことで、実は未着手になっていること、すなわち可変的な部分を見出す方法が有効です。このような対話は実に骨の折れる作業ですが、丹念にやれば効きます。必ず効きます。
“工数的な制限をいったん無視して考える”というのは、“そんなことに取り組み始めたら時間がいくらあっても足りない”という思い込みを切り崩すことを意味します。寝ないで仕事しろ!ということでは決してありません。やりたくても手が足りないのであれば変革推進チーム側がその実行をフォローすることもできます。他部署から人を借りてくることも可能です。工数不足ならば何とか手当てをするから、やるべきことを洗い出しましょう、と働きかけるのです。そうすることで、本来の改善余地とその実現に必要な工数とを切り分けて議論が出来ます。実際、私もそうしました。そして改善余地は大きいが取り組むには手がかかる施策は、我々推進チームもフォローし、経営陣と協議し他部署の方々をアサインして頂き、きちんと仕上げていきました。
サプライチェーンのありたい姿への変革
このように課題を一つずつ明らかにし、一つずつ解決策を考案し、少しずつ実施できるようになった後、より大きなチャレンジに向き合っていくことになります。既存業務プロセスの変更という大きなチャレンジに。
私が担当したこのプロジェクトでも、現行プロセスを変更するところで壁にぶつかりました。“こんな風に変えた方が良い”という方針は描けても、実業務に落とすとなると、“本当に問題はないのか”、“現場や他部署の理解は得られるのか”という懸念から、もう一度考え直してから決めたいなどの慎重な意見が噴出し、仮説検証が一向に進まないということが多々ありました。読者の皆さんが扱った変革プロジェクトでもご経験があるかと思います。
この打破に必要なのは“検証すべきことを明確にすること”と、“小さく始めること”の2つです。“変えてしまって本当に問題は無いのか”という問いに対する正解などありません。それを会議室で議論していても何も変わらないし、何も生まれません。ですので、“まずここまで検証出来たら次に移る”という段階的アプローチにすることを提示し、現場レベルでは具体的な段階の切り方を個別協議の場で詰め、経営陣とも具体的に握り、挑戦への安全弁を設けた上で背中を押すことが重要です。
合わせて重要なことはファーストステップを低く設定して、“小さく始める”ことです。“小さく始める”がいったん動き始めると、活動を通じて小さな成功体験が積み上がり、次はここ、その次はここ…、という動きに繋げやすくなります。
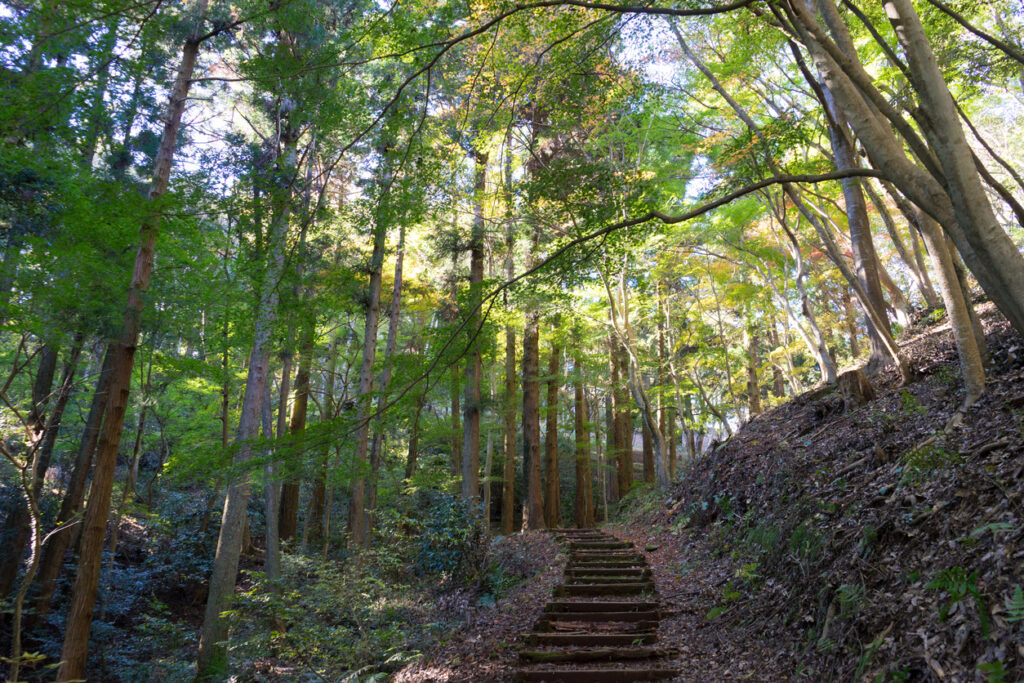
成果創出のカギは説得ではなく納得
実はこの企業では以前にも同種のサプライチェーン変革に取り組みながらも、成果を出すことができていませんでした。サプライチェーン変革は手を打った時から成果発現までに時間がかかります。成果が発現しないと変革の効果が実感できず、効果が実感できないことが“こうしていこう”と決めたはずの施策を中途半端なものにしてしまい、なし崩し的に終わってしまっていた、とのことです。トップダウンが強すぎて現場が本音の部分ではついてきていなかった面もあったと、後に伺いました。
私が携わったこのプロジェクトは、関係者各位の多大なるご尽力のおかげで大きな成果を創出することができました。このプロジェクトも途中で頓挫しかけたことが幾度となくありました。それはまさに上述したサプライチェーン変革の特性によるものでしょう。しかし我々は途中で諦めることをしませんでした。私は“改革に関わる最後の一人になってもやり続ける”という強い決意で臨んでいました。今思えば、私が貢献できたと胸を張れることはその決意だけだったのかもしれません。
実は二度目であったサプライチェーン変革が奏功したのは、壁にぶつかりながらも諦めずに取り組み続けた関係者のご尽力あってのことです。私がしたことはお膳立てと粘り強い対話だけです。
高すぎる山などない。深すぎる谷などない。渡れない川などない。そう実感します。